Automation-aided railroad inspection technologies offer the potential to boost safety and save lives while improving the efficiency and effectiveness of current track maintenance and inspection practices, according to a new study issued by the U.S. Department of Transportation’s Volpe National Transportation Systems Center.
[Above photo by the FRA.]
The Federal Railroad Administration asked a Volpe Center human factors team to “research visual and automation-aided” rail inspection processes to identify factors that could lead to hazards during both types of inspections and provide recommendations to mitigate such risk factors.
The study request comes on the heels of a final rule issued by FRA on August 28 that allows railroads to use ultrasonic inspection technology, augmented with global positioning system technology, to employ continuous rail testing.

“These modernized standards will allow railroads to implement innovative inspection methods without the burden of applying for individual waivers with well-established safety records,” added FRA Administrator Ronald Batory in a statement at the time.
According to a separate statement, the Volpe Center said its research team focused on railroad inspection systems that use automated track geometry technology for its study – a widely used form of automation-aided track inspection used in freight and passenger rail.
The team studied three sociotechnical systems, where “sociotechnical system” refers to a combination of people, technologies, actions, and feedback that comprise the inspection process:
- Visual inspection sociotechnical system: Only using visual inspection practices to find track issues.
- Track geometry measurement systems or TGMS and visual inspection sociotechnical system, using both together to find track issues.
- Autonomous track geometry measurement systems or “aTGMS” and visual inspection sociotechnical system: using both together to identify track issues.
The Volpe Center said it used existing literature, information from multiple site visits, as well as additional discussions with subject matter expects to identify and document how the track inspection process works, including the role of the inspector, the role of automation, and the types of human-technology interaction required.

The team also sought to understand what railroads do once rail defects are located and how the inspection process fits into the broader track lifecycle, which includes inspection, maintenance, and operations.
During its analysis, the Volpe Center team identified how each action in the inspection process could lead to undesirable conditions, or hazards. The team then developed a comprehensive set of scenarios describing how combinations of factors could lead to undesirable events or accidents.
By identifying ways to address contributing factors from these scenarios, the Volpe Center then developed recommendations addressing potential risks at various stages of the track inspection process – i.e., detecting, assessing, and fixing defects – as well as different levels of the sociotechnical system, such as task, individual and team, organizational, tools and technology, physical environment, and external factors.
Major themes that emerged from those recommendations include the need for strong user-centered design when incorporating new technologies, the value of hands-on training, the importance of communication and coordination, and a need to manage the impact of production and resource pressures on inspection and maintenance activities, the Volpe Center said.
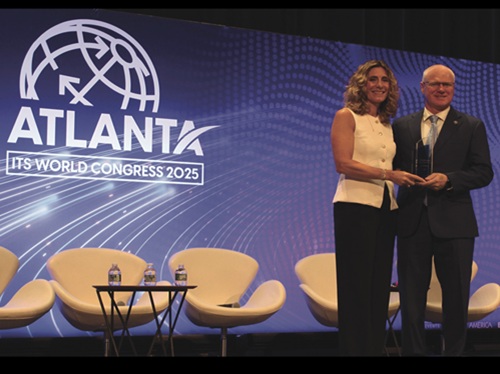
Georgia DOT’s McMurry Wins ITS Lifetime Award
August 29, 2025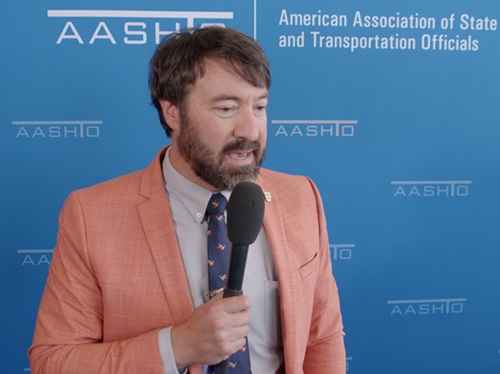