A recent innovation developed by the Arizona Department of Transportation’s Nogales Maintenance Unit is making roadway guardrail repair easier and safer for its highway crews.
[Above photo by the Arizona DOT]
The device (seen above) – called a “guardrail crab” – reduces the potential for arm, leg, and back injuries while also speeding up the guardrail installation process, reducing traffic exposure for highway crews.
The agency said in a blog post that each guardrail is 25 feet long and weighs 185 pounds. Previously, for proper installation, at least four crewmembers were required to hold the guardrail in place roughly 20 to 30 inches from the ground for two to seven minutes.
Now, by using two guardrail crabs, crewmembers can line up the guardrail at the site and move it into place. Not only has this reduced the number of crew members needed for guardrail repairs, it has increased safety for employees and reduced time working on busy roads.

This innovation is also partly a result of the “kaizen” continuous improvement philosophy Arizona DOT established in 2016.
“A ‘kaizen’ can be large or small. It can be a new way of removing rusted nails from damaged guardrails with an impact gun and 6-inch socket to a new invention called a guardrail crab, which moves and lifts guardrail into position along a roadway,” explained Arizona DOT Director John Halikowski in a separate blog post.
“The result has been a reduction in the number of employees needed to replace guardrail and potential injury, not to mention enhancing safety for everyone,” he noted.
“I’m proud to say that we’ve implemented more than 39,000 ‘kaizens’ over the past six years,” Halikowski added. “We’ve made changes for the better – eliminating wastes, improving processes, enhancing safety and quality, and providing better customer experiences.”
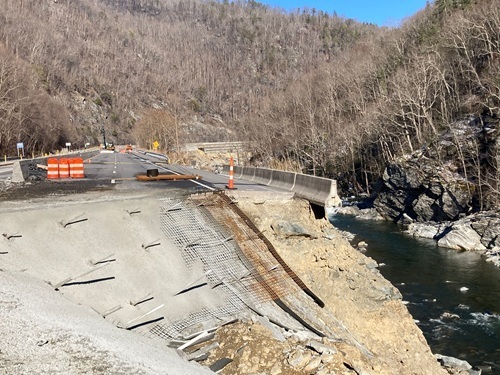
NCDOT to Rebuild I-40 with National Forest Rocks
June 27, 2025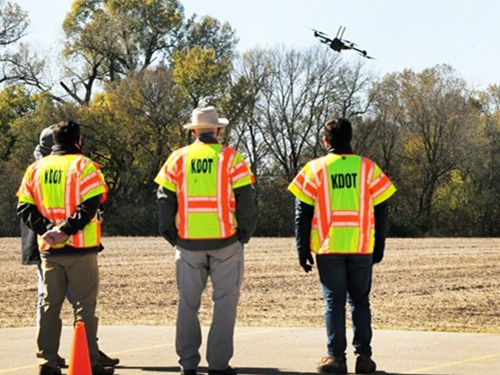