A recent blog post by the Texas Department of Transportation provided an inside look at the division within the agency responsible for ensuring all of the materials used in statewide roadway construction projects meet strict quality standards.
[Above photo by TxDOT]
TxDOT’s Materials and Testing Division or MTD team conducts essential tests using several technologies to ensure all roadway materials — concrete, asphalt, etc. — meet those standards.
A key service offered by the division’s laboratories is petrographic analysis; a method used to identify why materials fail to meet industry standards.
Using medical equipment, lab technicians analyze microscopic particles that are invisible to the human eye, allowing them to assess material chemistry and provide crucial information to TxDOT engineers about defective materials.
“We test to ensure that by meeting specification requirements, we are ensuring safety on our TxDOT projects,” explained Ryan Barborak, TxDOT’s MTD director, in the blog post.
He explained that, as his team’s testing regime involved everything improving road sign reflectivity for better night visibility to ensuring pavement quality, they have “a direct impact” on motorist safety.
Other state departments of transportation use similar laboratory facilities.
For example, the Nevada Department of Transportation relies on its lab to ensure asphalt compounds can withstand the high summer heat that affects most of the state’s roads – ensuring roadway materials can withstand 168 degrees Fahrenheit.
That material testing includes steel as well as concrete and asphalt, as explained in the New Jersey Department of Transportation video below.
The agency tests samples of steel “rebar” – short for “reinforcing bar” – before it is sent to infrastructure project to ensure that steel product meets or exceeds industry standards.
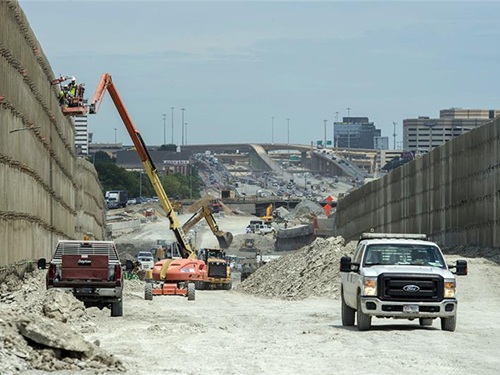
Texas Unveils Decade-Long $146B Transportation Plan
August 29, 2025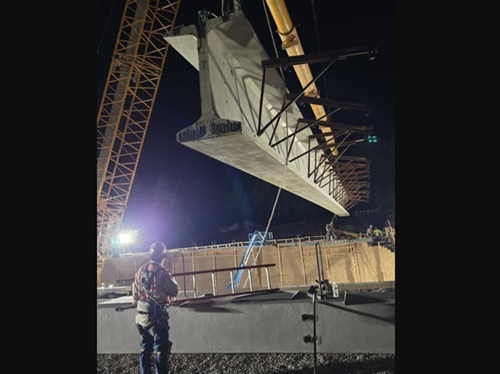