The Idaho Transportation Department (ITD) recently began applying a new “hot chip seal” process to more than 100 lane miles in the heart of Boise; a process that allows its highway crews to work at night, minimizing disruptions for roadway users.
[Above photo by ITD]
The agency noted in a statement that traditional “chip seal” processes use oil heated to around 150 degrees that can be applied during daytime high temperatures. By contrast, with “hot chip seal,” oil is heated to 300 degrees so it can be applied during nighttime lows.
That also creates a “fast seal” side effect, meaning motorists can use the roadway within 30 minutes of hot chip sealing, compared to the 24-hour wait required by traditional “chip seal” methods.
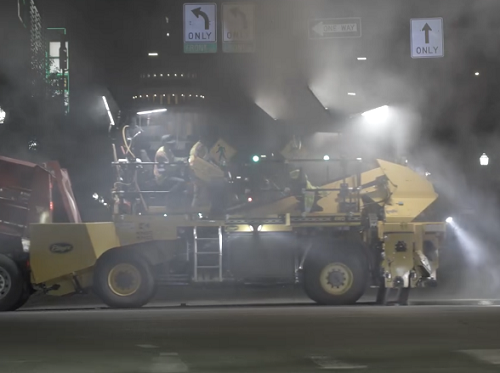
Thus the high-temperature “hot chip seal” process not only extends the pavement’s service life but also minimizes disruptions to businesses and motorists, ITD noted.
Concurrently, the Washington State Department of Transportation recently detailed in a blog post what the overall benefits of “chip sealing” are when it comes to roadway repairs and preservation goals:
- Protects the pavement: It acts as a waterproof barrier, shielding the road base from water damage, which is a major cause of cracks and potholes.
- Safety benefits: The embedded chips create a textured surface, enhancing traction for vehicles, especially in wet weather. It also provides and anti-glare surface during wet weather.
- Cost-effective: Compared to a complete road repaving, chip seal is a much more affordable way to extend a road’s lifespan by several years.
- Not only does chip seal preserve road surfaces, it also improves traveler safety. The protective coat restores traction to prevent skidding, particularly on wet roads. It helps visibility by providing an anti-glare surface during wet weather.
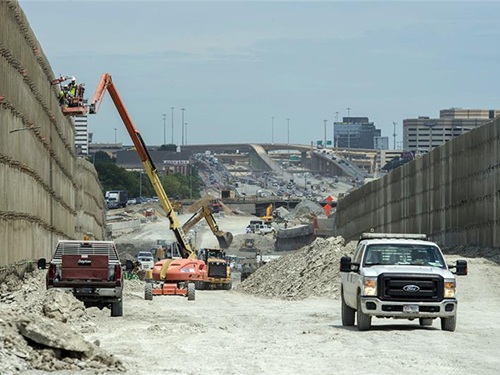
Texas Unveils Decade-Long $146B Transportation Plan
August 29, 2025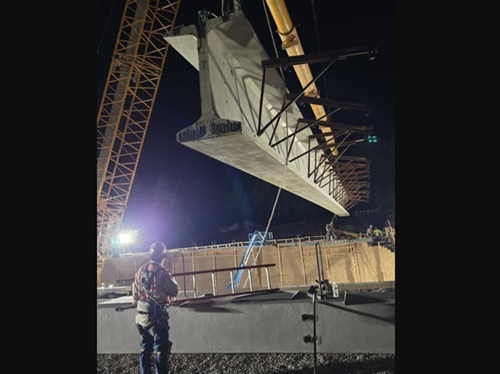